Have you ever asked yourself how much money is going out the window by using an outdated warranty management system, or even worse, using spreadsheets or not even tracking them at all because of the complexity of the process? It is no secret that effectively managing the warranties and claims of your fleet is an essential part of any profitable company. Thankfully, the management of your warranties can be made easy with a good CMMS software.
Here is everything you need to know about warranty management.
What is a Warranty Management Software for Fleets and Heavy-Duty Shops?
Having a Computerized Maintenance Management System (CMMS) with a warranty management system is essential for efficient warranty management. It can have an immense impact on a company’s fleet profits. A warranty management software helps companies create, track and manage warranties and claims for their fleet or heavy-duty shop. It will automate and track all your warranty and claims processes to optimize your time, lessen man-made errors and ensure that all of your warranties are used to the maximum. There can be multiple types of warranties managed with a warranty management system, but here are the main ones: General warranties, extended warranties, parts warranties and external service warranties for all your trucks and equipment. Here’s how we would best describe each type*:
General warranties: warranties that you would get at the purchase of a new unit or asset.
Extended warranties: an extension of a pre-existing warranty on a unit.
Parts warranties: warranties that your parts supplier will give you at the purchase of a part.
External service warranties: is a warranty on a repair that was performed by an external service supplier.
*The terms of these warranties can be different depending on your supplier.
5 Simple Steps to Optimized Warranty Management with Heavy-Duty Shop Management Software
1. Make sure you have the ability to create a warranty profile per unit. This will allow the system to know the terms of the warranty of each unit (since they can be widely different). It will be the base for your warranty tracking.
2. A good warranty management system should track multiple levels of warranties. Your system should be able to track general, extended, parts and external services warranties. This will bring optimal savings to your business and provide you with a return on investment (ROI) that will cover a significant portion of the costs of acquiring maintenance software.
3. Make sure that your system uses automation. First of all, it should be able to recognize that a part or unit you are working on is under warranty and have automated pop-ups that would notify the user. The use of an automated colour coding system is also key to being able to quickly identify when something is under warranty. These automation features are very important since they will make it impossible for users to neglect important steps.
4. Look for a tool that will provide complete traceability. Being able to prove when the part was bought and the exact time it was installed will permit you to initiate the claim process for parts warranties at the installed date, instead of the date of purchase.
5. Make sure that your system can automate your warranty claims management. A good CMMS software will automatically create claims forms and fill out the required information. You should also be able to track all of your claims by coloured-coded statuses for easy follow-ups.
What is the Process of Warranty Management in a CMMS Software?
When using a good fleet maintenance software, your warranty management is made easy. Here is an example of what your warranty management process should look like.
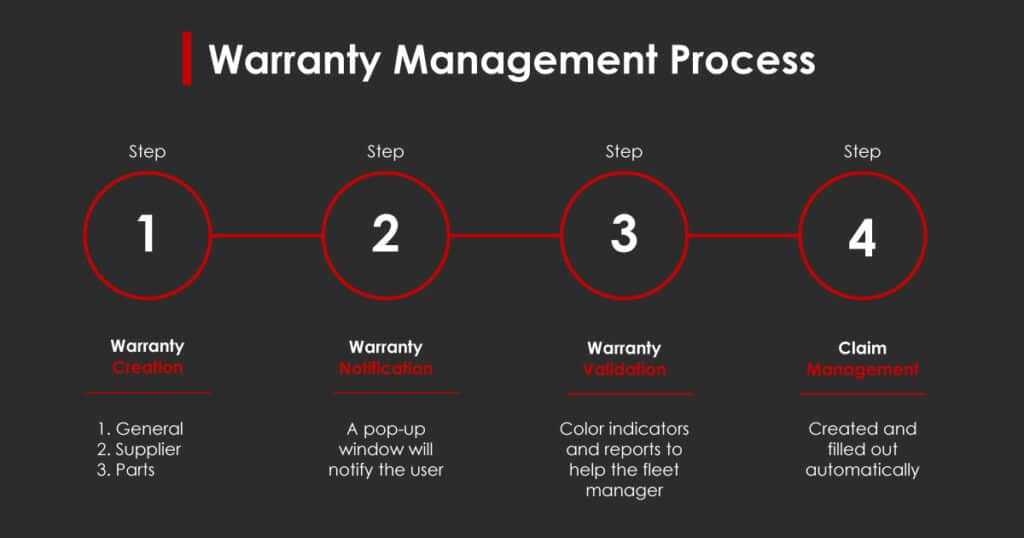
1. Create a Warranty Profile
A good software should include a unit profile. In this profile, you will add any important information about your unit: model, year, brand, owner, location, maintenance profile, inspections, warranties and many more. By having warranties entered for each unit, the software will be able to track them using the odometer (with a GPS telematics integration) or simply by tracking the expiration date of the warranty. For example, your warranty could be for 1 year 60 000 km.
2. Notification
When a mechanic wants to work on a unit under warranty, the system will send a pop-up window informing the user that the unit or part they just put into the system is under warranty. The same information will be provided for external service warranties, along with the name of the supplier with whom the warranty is.
3. Validation
At the end of the day, the foreman, chief mechanic or fleet manager will usually validate all the work orders to ensure that all the right parts, times and names are on the work orders. Once they are validated, he will simply close them. During this process, it is important that he can easily locate any part, unit or external service under warranty with a colour coding system. If any warranties were missed on a part, for example, the fleet manager could then place said part on the claims shelf for claiming.
4. Claiming
When using a warranty management system, the claiming process should be automated. A claims form should be automatically created when a part or unit under warranty is put on a work order. With a good CMMS software, all of the necessary information will transfer automatically on your supplier’s claim form with just a few clicks. You can then send it via email with the PDF attached without having to enter anything manually. You should also be able to follow the status of your claims with a colour-coded system.
Ready to take your warranty management to the next level? Request a demo now: