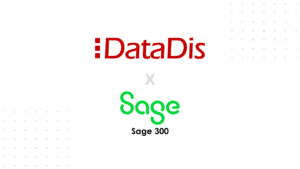
MIR-RT is the #1 specialized software designed for any heavy-duty repair shop that wants to take their maintenance management to the next level. With our seamless integrations, you will increase your shop’s productivity, reduce your maintenance costs and centralize every aspect of your operations.
Join Hundreds of Satisfied Repair Shop Owners
Are rising operational costs affecting your repair shop’s profitability? With MIR-RT’s advanced cost tracking features, shop managers can gain comprehensive insights into maintenance expenses and shop operations. Our heavy-duty repair shop management software provides detailed reports on costs related to parts, labor, and other operational expenses. By analyzing this data, you can identify inefficiencies, optimize resource allocation, and implement cost-saving measures to enhance your bottom line. MIR-RT empowers you to make informed decisions that drive financial efficiency and maximize your repair shop’s performance.
“We like the user-friendliness of MIR-RT’s user interface. The ease with which work orders can be created and tracked and the clarity of the reports generated are undeniable strengths. The functionalities of task scheduling and inventory tracking are extremely useful in optimizing our maintenance operations.”
“First, we appreciate the quality of the training provided to help us use the software optimally. We also value its user-friendliness, thanks to the interface and tools it offers, such as tags for identification. Tracking services performed for clients is very easy and efficient.”
“The management of work orders, inventory, and billing is an aspect of the software that we appreciate and use every day. One of MIR-RT’s strengths, in my opinion, is the real-time mode managed with a scan/tag system for our mechanics. As a heavy vehicle repair center, this allows us to accurately assess the repairs performed by our team and effectively evaluate our productivity. It’s also easy to retrieve information for our customers.”
Our heavy-duty repair shop maintenance software seamlessly connects with the tools you already use, such as accounting systems, parts order platforms, and more. MIR-RT reduces manual entry and ensures data consistency across your operations. This unified approach not only saves time but also improves accuracy and productivity, allowing you to focus on what matters most – repairing your clients’ heavy vehicles and equipments quickly.
Are your technicians finding it challenging to stay productive while juggling tasks both inside and outside the garage? With our MIR-RT Web Mechanic Mode, your team can work seamlessly from anywhere, at any time, whether they’re diagnosing issues in the shop or performing roadside repairs. By providing technicians with easy access to the tools they need remotely, you’ll boost productivity and streamline workflows. Empower your team to manage tasks on the go, improving efficiency and ensuring quicker turnaround times for all repair jobs.
Take Control of Your Heavy-Duty Shop With
MIR-RT Software
The Top Rated Maintenance Software to reduce your maintenance costs and increase your fleet safety.